For airlines operating fleets of up to ten aircraft, good engine condition is the backbone of their entire operation. Unlike larger airlines with deep pockets and the ability to absorb dispatch failures, smaller operators face far more significant consequences when a single airplane is grounded. Engine Maintenance Consulting directly impacts dispatch reliability, operational reliability, flight schedules, and – most importantly – operating cost. A grounded plane means lost revenue, disrupted service, and potentially disgruntled customers. Every flight counts for small airlines, which makes keeping aircraft engines in the best possible condition not just a priority but a necessity.
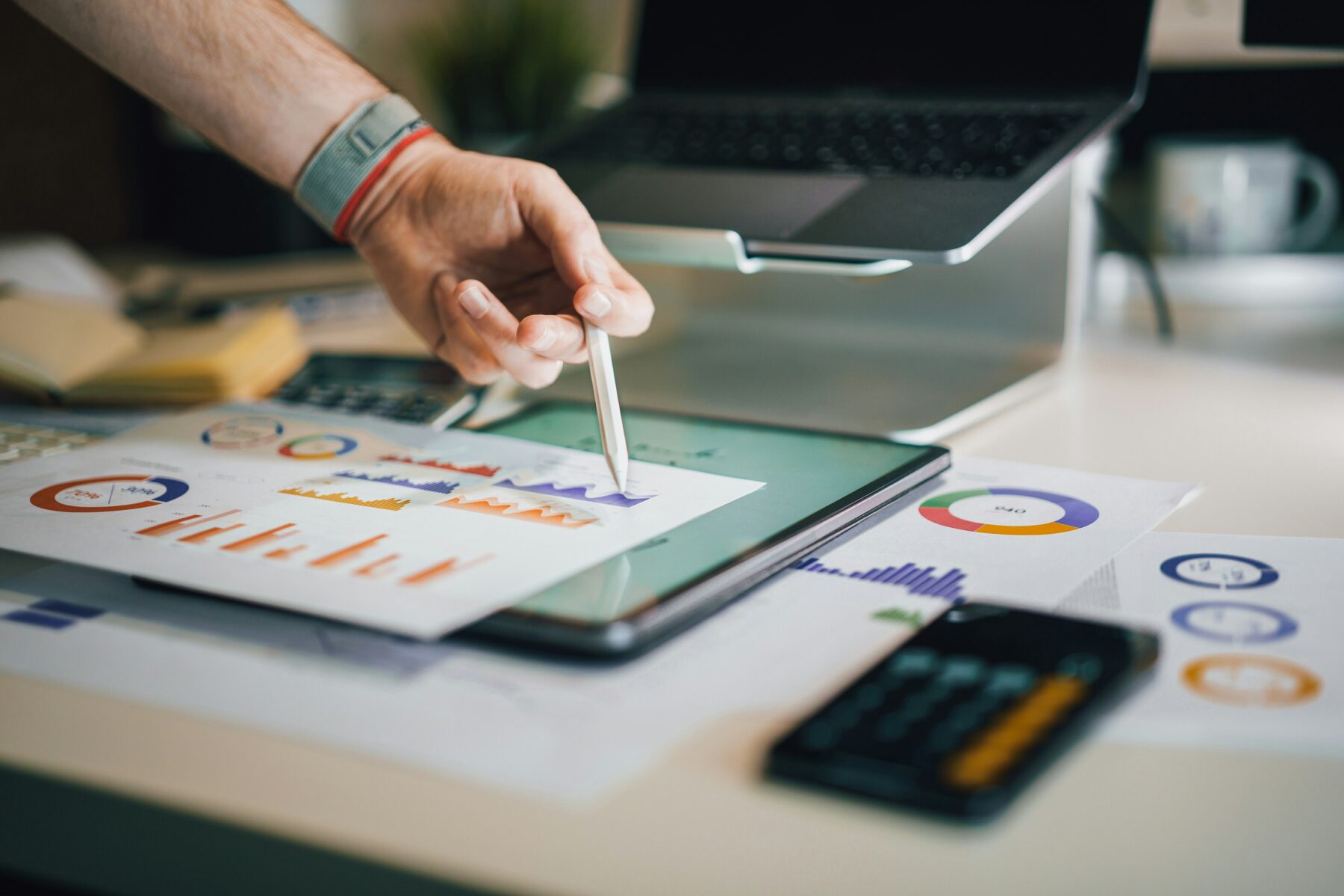
1. Why Engine Maintenance is Critical for Airlines
Small airlines also face unique challenges when managing their engine maintenance. With fewer aircraft, there is less flexibility to cover for downtime, and unexpected maintenance events can quickly throw a wrench into operations. For these reasons, small airlines must be more strategic in their maintenance approach, ensuring that their fleet remains reliable and their costs predictable. This is where a proactive engine maintenance strategy can make all the difference.
Small airlines are particularly vulnerable to a number of common, yet avoidable, engine damage scenarios. Deferred maintenance is a common trap—where airlines delay minor repairs (which may be done during base maintenance) to avoid immediate costs, only to face much larger maintenance event cost down the line. Neglecting routine checks – such as borescope inspections – or deferring necessary repairs can lead to significantly higher engine wear and tear, often requiring early engine removals. For smaller fleets, these unexpected and unplanned repair charges can be catastrophic, turning what seemed like minor savings into major financial setbacks.
Other common traps include ignoring manufacturer recommendations for engine maintenance, which often leads to premature wear and tear, and underestimating the impact of component degradation. As engines accumulate flight hours and flight cycles, their performance naturally degrades, and if this goes unmonitored, the risk of failure increases. These issues, however, can be prevented through proactive maintenance strategies – such as engaging with Engine Condition Trend Monitoring (ECTM) – which focus on early detection and timely intervention.
The Benefits of Engine Maintenance Consulting (EMC)
This is where Engine Maintenance Consulting (EMC) services come into play. For small airlines, working with an Engine Maintenance Consulting firm will – in most cases – help avoid costly surprises, simply because a consultancy or an individual with a sole focus on aircraft engines and the necessary experience will make sure that the right decisions are taken at the right time with the owner’s/operator’s savings in mind. EMC firms offer expert advice on everything from creating customized maintenance schedules to monitoring engine performance data in real time, allowing airlines to make informed decisions, perform preventive maintenance avoiding engine damage before it happens.
Early consultation with EMC providers can also help small airlines manage their budgets more effectively. Rather than reacting to unexpected engine removals, EMC services focus on proactive, data-driven maintenance planning that minimizes surprises and maximizes cost efficiency. From helping airlines understand their total cost of ownership and operation to negotiating favorable maintenance contracts, EMC providers play a critical role in supporting the long-term success of small airlines.
By partnering with an EMC provider, small airlines can ensure a smooth and efficient operation with minimal downtime – ultimately protecting their profits and maintaining high levels of dispatch reliability.
2. Understanding the Risks: Cost Traps in Engine Maintenance
For small airlines, with only a handful of planes, the stakes are high when it comes to engine maintenance. Minor mismanagement can lead to significant cost increases at shop visit time and drain financial resources. It is crucial for small operators to understand the common cost traps like unscheduled engine removals, work scope escalations, parts availability and how to avoid them. By recognizing these risks early and taking proactive action, small airlines can protect their bottom line and keep their fleet operating smoothly.
Deferred Maintenance: A Risky Gamble
One of the most tempting traps small airlines fall into is deferred maintenance. It may seem logical to delay certain maintenance tasks to save money in the short term, especially when budgets are tight. However, this approach backfires in most cases. What starts as a minor issue (e.g. cracks in combustion liner) can quickly escalate into a major engine failure (combustion liner material detaching causing significant downstream damage), increasing cost by multiples of an initial repair and leading to extended downtime.
The lesson is clear: while deferring maintenance might offer short-term relief, it often leads to long-term financial pain. Small airlines must prioritize regular maintenance to prevent small problems from spiraling into expensive shop visits.
Not following Manufacturer Guidelines
Another mistake operators make is ignoring the maintenance guidelines set by the engine’s Original Equipment Manufacturer (OEM). These guidelines are not just recommendations – they are essential for maintaining the engine’s performance and longevity. When small airlines overlook or bypass OEM standards, they expose their engines to unnecessary risks, including premature wear, tear, and failure.
OEMs provide precise instructions on how and when to perform maintenance on specific engine models, based on extensive testing and operating data. Deviating from these guidelines—whether it is extending the time between inspections or using unapproved parts – can significantly increase the likelihood of engine failure. Moreover, ignoring OEM guidelines can void warranties, leaving airlines solely responsible for costly repairs.
An Engine Maintenance Consulting (EMC) services provider can play a crucial role in ensuring that small airlines adhere to these manufacturer standards. EMC experts help airlines stay on track with OEM recommendations, offering peace of mind that engines are being cared for correctly and that costly omissions or misinterpretations are avoided.
Underestimating Component Degradation
One of the most overlooked aspects of engine maintenance is the gradual degradation of engine components. Over time, as engines accumulate flying hours, critical parts such as hot section components and bearings begin are exposed to attrition. For small airlines, monitoring the deterioration, e.g. through borescope inspections, is essential in avoiding unscheduled removals and the high repair costs associated with them.
The financial impact of unmonitored component degradation can be devastating. For example, if a turbine blade is allowed to degrade past its safe operating limit, it could fail in-flight, requiring not only expensive repairs but also grounding the aircraft for extended periods. Such an event could lead to lost revenue from canceled flights, as well as potential damage to the airline’s reputation.
3. The Role of Early Consultation in Preventing Engine Damage
Preventive maintenance, driven by real-time data analytics, is a powerful tool in combating component degradation. By using data to predict when parts will fail, airlines can replace them before they cause damage, minimizing downtime and avoiding the cost of unexpected repairs. An EMC provider can offer small airlines the expertise and tools needed to implement predictive maintenance strategies, ensuring that engines remain in optimal condition.
Proactive vs. Reactive Maintenance: The Cost Difference
PThe difference between proactive and reactive maintenance can be measured in both dollars and downtime. Reactive maintenance—waiting for something to go wrong before addressing it—may seem lower cost in the short term, but it often leads to bigger, more expensive repairs. For small airlines, which depend on every aircraft being operational, reactive maintenance can disrupt schedules and drastically increase maintenance costs.
On the other hand, proactive maintenance, which is based on regular inspections and early interventions, helps catch potential problems early. For example, instead of waiting for an engine part to fail, early consultation allows experts to identify wear and tear and schedule timely replacements, avoiding costly breakdowns. A comparative analysis of maintenance costs shows that airlines employing proactive strategies save significantly on repair bills over the long term. Early consultation with an EMC provider ensures that small airlines avoid the trap of reactive maintenance and instead focus on prevention.
Comprehensive Engine Health Monitoring
EOne of the key benefits of early consultation is the implementation of comprehensive engine health monitoring, such as Engine Condition Trend Monitoring (ECTM). In many cases small airlines do not have the in-house resources to consistently track engine performance metrics, but EMC providers can step in with advanced data analytics and monitoring tools. These tools continuously assess engine performance, tracking key indicators like Inter Turbine Temperature (ITT), Exhaust Gast Temperature (EGT), the pressures p2 and p3, and vibration levels to predict when components might fail.
The analysis of real-time data not only helps avoid immediate failures but also allows for strategic planning of maintenance schedules, e.g. by staggering of engine removals. For example, an EMC services provider can use predictive analytics to identify that a specific engine part will likely need replacement e.g. within the 500 flight hours, allowing the airline to budget and schedule the repair during a planned downtime, rather than dealing with an emergency repair during peak season.
Avoiding the One-Size-Fits-All Approach
Small airlines often don’t have the luxury of adhering to the same maintenance strategies used by large airlines with hundreds of aircraft. Compared with a large operation, the impact of one grounded aircraft in a small fleet will be more significant, which is why a tailored approach to maintenance is essential. One-size-fits-all approaches to engine maintenance can lead to unnecessary and inefficient practices that may not suit the operational realities of smaller airlines.
Early consultation with an EMC services provider helps airlines avoid these pitfalls by developing maintenance strategies that are specifically tailored to their needs. This might include adjusting for the type of aircraft in operation, the typical flight routes, and the unique conditions under which the airline operates. By working with an EMC provider, small airlines can ensure that their maintenance approach is optimized for their fleet, reducing costs, and maximizing aircraft availability.
4. How Engine Maintenance Consulting Services Help Small Airlines Manage Costs
For small airlines, managing engine maintenance costs effectively is critical to sustaining profitability. With fewer aircraft in their fleet, these airlines are particularly vulnerable to unexpected expenses and operational disruptions. Engine Maintenance Consulting (EMC) services offer a range of solutions that not only help small airlines reduce the risk of costly surprises but also enable them to better forecast and control their engine maintenance events. From negotiating favorable one-off to long term maintenance contracts to optimizing the supply chain, EMC providers can deliver significant financial and operational benefits.
Budget Predictability Through Expert Consulting
One of the most significant advantages of working with an EMC provider is the ability reduce the number of unscheduled removals in order to achieve budget predictability. Many small airlines struggle with unexpected maintenance costs, which can strain financial resources and disrupt cash flow. Early consultation with an EMC provider helps airlines gain a clearer picture of their long-term maintenance requirements and expenses.
EMC experts conduct thorough engine health assessments (e.g. borescope inspections, review of tech records of shop visits) and they can elaborate maintenance schedules that align with the airline’s operational needs. This approach not only prevents unscheduled removals but also helps airlines budget more accurately for routine and long-term maintenance. By understanding the total cost of ownership for engine maintenance – including parts supply, labor cost, and potential downtimes – small airlines can plan more effectively and avoid financial shocks.
Negotiating Maintenance Contracts
Establishing engine maintenance contracts can be a serious challenge for any airline, particularly when negotiating with large maintenance service providers or engine OEMs. Without expert guidance, airlines may end up in a commitment to an unfavorable contract with hidden fees, costly penalties, or restrictive terms that don’t cater to their specific needs.
An EMC provider brings valuable expertise to the negotiation table. With in-depth knowledge of industry standards and pricing models, EMC consultants can help small airlines secure better terms in their maintenance agreements. This may include preferential parts pricing, the option to supply parts, negotiating lower hourly rates, extended warranties, or more flexible service schedules that accommodate the airline’s operational patterns. By avoiding common contract pitfalls, small airlines can significantly reduce maintenance costs while ensuring high-quality service for their engines.
Optimizing the Maintenance Supply Chain
Efficient management of the maintenance supply chain is essential for small airlines that can’t afford prolonged aircraft downtime. However, maintenance planning and securing the right parts and services at the right time can be a logistical challenge. Delays in sourcing parts or scheduling maintenance can lead to aircraft being grounded, which directly impacts revenue and operations.
EMC providers offer a strategic advantage by streamlining the supply chain. In most cases they have established relationships with parts suppliers, repair shops, and OEMs, allowing them to secure critical components faster and at better prices. Additionally, EMC consultants can help small airlines plan ahead for scheduled maintenance, ensuring that parts are available when needed and minimizing the risk of delays. This proactive approach reduces downtime and associated costs, keeping aircraft in the air and generating revenue.
5. Case Studies: Success Stories from Small Airlines
Since airlines operating less than ten aircraft usually do not have a dedicated powerplant engineering, selecting the right Engine Maintenance Consulting (EMC) partner is a critical decision for small airlines looking to reduce operating costs through preventive engine maintenance. The right partner can help streamline maintenance processes, minimize downtime, and optimize engine performance – all while ensuring compliance with manufacturer recommendations and safety regulations. Below are key factors small airlines should consider when choosing an EMC provider, along with the long-term benefits of making the right choice.
Early Consultation Avoids Major Engine Overhaul
A small regional airline operating a fleet of six aircraft faced an unexpected engine malfunction that could have led to a $500,000 overhaul. The airline, lacking in-house expertise, turned to an EMC provider for an early consultation. Through a thorough engine inspection and performance analysis, the EMC team discovered a developing issue with a critical component. Instead of waiting for a costly, full-scale inspection and cost estimate, the EMC specialists recommended a minimum workscope repair, which was completed during a scheduled maintenance window.
As a result, the airline pushed back on the requirement for an extensive overhaul, saving both time and a significant amount of money. By acting early and proactively, they minimized downtime, preventing flight cancellations and maintaining their reputation for reliability.
Customized EMC Solution Saves 20 % on Maintenance Costs
Another success story involves a small airline with a fleet of eight aircraft. The airline faced rising maintenance costs and struggled with frequent unscheduled engine removals, which impacted their budget, cash-flow and operational efficiency. After partnering with an EMC provider, the airline underwent a detailed fleet analysis. The EMC team developed a customized maintenance plan that was tailored to the airline’s specific usage patterns, operational demands and engine fleet.
This tailored approach not only reduced unnecessary maintenance checks but also optimized the timing of engine inspections and repairs. Within the first year, the airline saw a 20 % reduction in overall maintenance costs. By aligning maintenance schedules with actual engine performance, they were able to avoid over-maintenance and reduce unscheduled removals, resulting in significant cost savings and improved fleet availability.
Predictive Analytics Prevents In-Flight Engine Failure
A third case highlights how predictive analytics from an EMC provider prevented a potentially catastrophic in-flight engine failure. A small airline with five aircraft integrated Engine Condition Trend Monitoring (ECTM) into their operations with the assistance of their EMC provider. The EMC team used predictive analytics to track engine performance data, identifying patterns of degradation that would have gone unnoticed in a typical visual inspection.
During a routine review of engine data, the EMC team flagged a sudden change in performance metrics for one of the aircraft’s engines. This anomaly suggested an imminent failure of a key component. The airline was able to ground the aircraft and address the issue before it led to an in-flight emergency. By preventing a failure that could have resulted in a forced landing or worse, the airline not only avoided major repair costs but also safeguarded passenger safety and protected its reputation.
6. Choosing the Right Engine Maintenance Consulting Partner for Your Small Airline
Selecting the right Engine Maintenance Consulting (EMC) partner is crucial for small airlines looking to manage engine health effectively and control maintenance costs. With fewer aircraft in the fleet, every maintenance decision has a significant impact on operations and budget. Here’s what small airlines should consider when choosing the best EMC provider.
When evaluating EMC providers, small airlines should focus on three main criteria: expertise, reputation, and scalability.
- Expertise in Small Fleets: Not all EMC providers have experience working with airlines that operate a smaller number of aircraft. Choose a provider that understands the unique challenges of managing a limited fleet and can tailor solutions to minimize downtime and optimize maintenance schedules.
- References and Track Record: Look for EMC firms with a proven track record in the aviation industry, especially those that have successfully helped airlines of similar size. Reviews, case studies, and industry recommendations can provide valuable insights into a provider’s reliability and effectiveness.
- Scalability of Services: Small airlines need flexibility. Your EMC provider should offer scalable solutions that can grow with your airline. Whether you’re planning to expand or simply need customized services, ensure that the EMC firm can adapt to your evolving needs.
Questions to Ask Potential EMC Providers
Before committing to an EMC partnership, it’s essential to ask the right questions to ensure the provider aligns with your airline’s needs:
- How do you tailor your services to small airlines? Understanding how the EMC provider customizes their maintenance solutions is critical. Avoid firms that offer a one-size-fits-all approach.
- What experience do you have with airlines of similar size? An EMC partner with relevant experience will be more capable of understanding the operational and budget constraints that smaller fleets face.
- How do you integrate real-time data and predictive analytics into your services? With engine health monitoring becoming more data-driven, ensure your provider uses advanced analytics to predict potential issues before they escalate.
- What is your approach to long-term cost management? Ask about strategies for maintaining budget predictability and how they help airlines control costs over time, rather than just focusing on short-term fixes.
Long-Term Benefits of an Ongoing Engine Maintenance Consulting Partnership
Choosing the right EMC provider isn’t just about immediate cost savings; it is about building a long-term relationship that evolves with your airline’s needs. A strong EMC partnership offers several long-term benefits:
- Proactive Maintenance and Reduced Downtime: By continuously monitoring engine performance and providing ongoing consultation, your EMC partner helps prevent costly breakdowns and minimize operational disruptions.
- Better Budgeting/Forecasting: With an EMC provider offering expertise in cost prediction, your airline can plan maintenance expenses more accurately, avoiding sudden financial surprises.
- Operational Efficiency: As your fleet grows or flight operations change, your EMC partner can adjust maintenance strategies to fit new demands, ensuring your airline operates at peak efficiency.
By considering these factors and asking the right questions, small airlines can ensure they select an EMC provider that not only fits their current needs but also supports long-term operational success and cost management. A strong partnership will safeguard your fleet, improve reliability, and protect your bottom line.
7. The Value of Early Consultation in Protecting Your Investment
For small airlines with up to ten aircraft, engine maintenance is not just a technical necessity—it is a critical component of financial health and operational reliability. Early consultation with an Engine Maintenance Consulting (EMC) partner offers invaluable benefits by addressing potential problems before they become costly issues. By taking a proactive approach, airlines can optimize their maintenance processes, minimize downtime, and ultimately protect their investment.
Summarizing the Financial and Operational Benefits
The financial and operational advantages of early EMC consultation are clear. Small airlines that engage with EMC providers early in the maintenance process benefit from:
- Cost Savings: By identifying and addressing issues before they escalate, airlines can avoid expensive repairs and overhauls. Predictive maintenance strategies reduce the likelihood of unscheduled engine removals and the associated costs.
- Operational Reliability: A well-maintained engine ensures fewer delays, cancellations, and unscheduled downtimes, which can significantly impact a small airline’s bottom line and reputation.
- Budget Predictability: EMC providers help airlines plan their maintenance budgets more effectively by offering tailored solutions that fit the specific needs of small fleets, avoiding unanticipated expenses.
- Customized Solutions: Unlike large airlines, smaller fleets benefit from highly tailored maintenance plans that consider the unique operational demands and financial limitations of each airline.
Next Steps: How to Begin Working with an EMC Provider
For small airlines looking to take the next step in safeguarding their fleet and optimizing costs, the path to finding the right EMC provider is straightforward:
- Research EMC Firms: Look for providers with proven expertise in working with small fleets and a reputation for delivering customized, data-driven solutions.
- Schedule an Initial Consultation: Early conversations with EMC providers will help you understand how they can tailor their services to your needs and how proactive maintenance strategies can be implemented. A table inspection performed during an ongoing engine shop visit, could be a low-cost starting point for a successful relationship with an EMC provider.
- Ask the Right Questions: Ensure the provider understands the unique challenges of operating a small fleet and can offer scalable, flexible solutions.
By engaging with an EMC provider early and taking a proactive approach to engine maintenance, small airlines can significantly enhance their operational efficiency, reduce long-term costs, and secure the future of their business.